What is Porosity in Welding: Usual Sources and Efficient Solutions
What is Porosity in Welding: Usual Sources and Efficient Solutions
Blog Article
Porosity in Welding: Identifying Common Issues and Implementing Best Practices for Prevention
Porosity in welding is a pervasive issue that frequently goes undetected up until it causes significant problems with the stability of welds. In this discussion, we will discover the crucial aspects adding to porosity development, examine its damaging results on weld performance, and discuss the finest methods that can be adopted to lessen porosity event in welding procedures.
Common Causes of Porosity
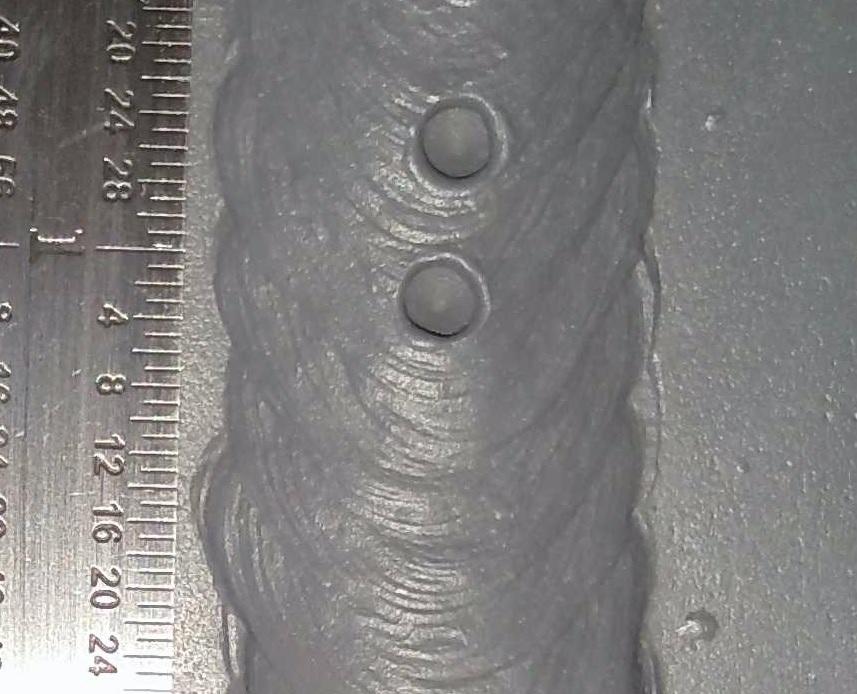
Making use of filthy or damp filler products can introduce contaminations right into the weld, contributing to porosity issues. To reduce these common causes of porosity, comprehensive cleaning of base metals, appropriate protecting gas choice, and adherence to ideal welding parameters are crucial practices in accomplishing high-quality, porosity-free welds.
Effect of Porosity on Weld Top Quality

The existence of porosity in welding can dramatically jeopardize the structural stability and mechanical residential or commercial properties of welded joints. Porosity creates gaps within the weld metal, damaging its general toughness and load-bearing capability.
Among the key effects of porosity is a decrease in the weld's ductility and durability. Welds with high porosity degrees often tend to show lower effect stamina and minimized capability to warp plastically prior to fracturing. This can be especially worrying in applications where the bonded parts undergo dynamic or cyclic loading conditions. Porosity can restrain the weld's capacity to effectively send pressures, leading to early weld failure and possible safety and security hazards in essential structures. What is Porosity.
Finest Practices for Porosity Avoidance
To boost the architectural stability and high quality of bonded joints, what particular actions can be applied to decrease the incident of porosity throughout the welding process? Porosity prevention in welding is crucial to ensure the stability and stamina of the final weld. One efficient practice appertains cleaning of the base metal, getting rid of any kind of impurities such as rust, oil, paint, or moisture that might bring about gas entrapment. Making sure that the welding tools is in great condition, with tidy consumables and proper gas circulation prices, can also dramatically reduce porosity. Additionally, maintaining a steady arc and managing the welding criteria, such browse around this site as voltage, present, and check my site travel speed, assists create a consistent weld swimming pool that reduces the threat of gas entrapment. Utilizing the right welding technique for the certain product being bonded, such as readjusting the welding angle and weapon placement, can better protect against porosity. Regular assessment of welds and instant removal of any kind of problems identified throughout the welding procedure are important methods to avoid porosity and generate high-quality welds.
Significance of Appropriate Welding Strategies
Carrying out appropriate welding methods is extremely important in ensuring the architectural honesty and top quality of bonded joints, building upon the structure of reliable porosity avoidance measures. Welding methods straight influence the general stamina and toughness of the welded framework. One crucial aspect of correct welding techniques is preserving the appropriate warmth input. Too much warmth can bring about boosted porosity as a result of the entrapment of gases in the weld pool. Conversely, not enough heat might lead to incomplete blend, producing prospective powerlessness in this page the joint. Additionally, using the proper welding parameters, such as voltage, current, and take a trip rate, is vital for accomplishing sound welds with very little porosity.
Furthermore, the choice of welding process, whether it be MIG, TIG, or stick welding, need to line up with the certain demands of the project to make certain ideal outcomes. Proper cleansing and prep work of the base steel, in addition to choosing the right filler product, are likewise crucial components of competent welding techniques. By adhering to these best techniques, welders can decrease the danger of porosity formation and generate top quality, structurally sound welds.

Evaluating and Top Quality Control Measures
Checking treatments are crucial to identify and avoid porosity in welding, making certain the toughness and durability of the last product. Non-destructive screening methods such as ultrasonic testing, radiographic screening, and aesthetic inspection are typically employed to determine potential problems like porosity.
Conducting pre-weld and post-weld assessments is likewise essential in preserving high quality control requirements. Pre-weld inspections entail verifying the products, devices settings, and sanitation of the workplace to stop contamination. Post-weld examinations, on the various other hand, assess the final weld for any kind of problems, including porosity, and confirm that it fulfills defined requirements. Implementing an extensive high quality control plan that includes complete testing procedures and assessments is vital to reducing porosity concerns and ensuring the overall top quality of welded joints.
Verdict
Finally, porosity in welding can be an usual problem that influences the high quality of welds. By identifying the usual reasons for porosity and carrying out ideal techniques for prevention, such as correct welding techniques and screening steps, welders can ensure excellent quality and dependable welds. It is crucial to focus on avoidance techniques to minimize the incident of porosity and preserve the stability of welded structures.
Report this page